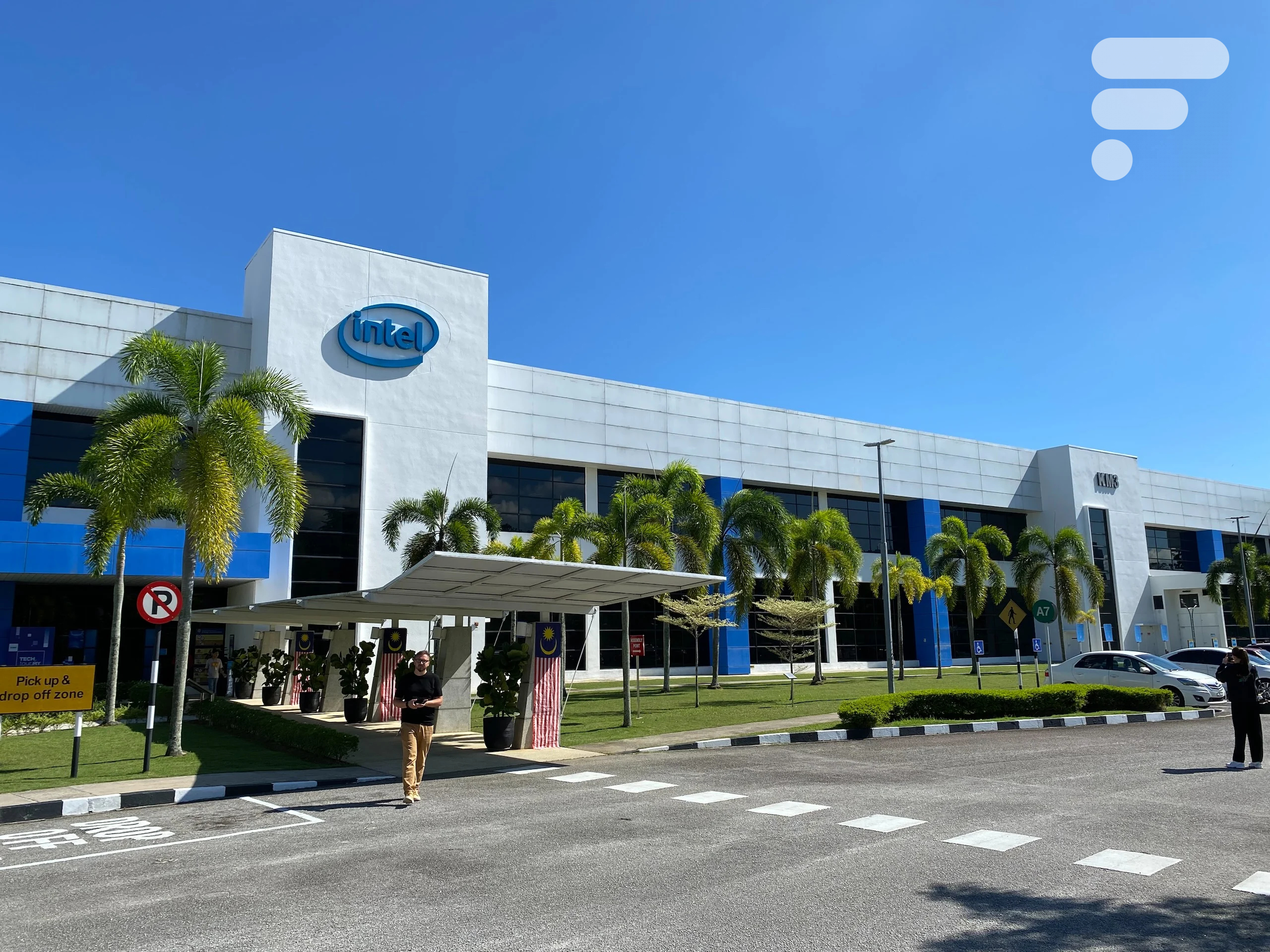
Pour la première fois depuis leur ouverture il y a 50 ans, Intel a récemment invité la presse à visiter ses usines d’assemblage, où les wafers deviennent des processeurs, en Malaisie.
Intel ouvre occasionnellement ses usines de fabrication de wafers, celles dans lesquelles il grave les puces sur des galettes de silicium. Mais il vient d’annoncer Meteor Lake, son premier processeur hétérogène produit en grande série. Un processeur Meteor Lake est effectivement constitué de plusieurs puces jointes, dont certaines sont produites par un autre fondeur, TSMC. Intel veut d’ailleurs lui aussi fabriquer pour d’autres clients, après des décennies de production exclusivement interne.
Dans ce contexte, le « packaging » (l’assemblage) prend beaucoup d’importance, ce qui explique que l’entreprise ait invité des médias du monde entier, dont Frandroid, à voir de leurs propres yeux comment ça se passe. En attendant de visiter, on l’espère, une usine de fabrication, nous avons donc visité les usines d’assemblage de Penang et de Kulim.
Première usine étrangère
Intel exploite aujourd’hui dix sites dans le monde, et douze demain, mais la Malaisie a la particularité d’être la première implantation étrangère du fondeur états-unien. En 1972, comme son rival AMD, il choisit Penang pour construire une première usine, qui assemblera l’Intel 8008, l’un des premiers microprocesseurs de l’histoire. Penang devient vite et demeure une place forte des semi-conducteurs.
Elle a beau avoir un régime autoritaire, du point de vue d’une multinationale attirée en premier lieu par la main-d’œuvre économique, la Malaisie présentait et présente plusieurs avantages par rapport à d’autres nations d’Asie du Sud-Est. Colonie britannique jusqu’en 1957, la Malaisie est largement anglophone. Elle forme en plus de nombreux ingénieurs. Et l’État de Penang en particulier dispose d’un port en eaux profondes, indispensable pour expédier la production.
Après 51 ans, alors qu’il y construit encore de nouvelles usines, dont sa plus grande salle blanche, Intel Malaisie emploie 15 000 personnes sur 4 campus et 16 bâtiments. Nous en avons visité quelques-uns.
Combinaison de lapin
Après une journée entièrement consacrée à Meteor Lake dans le centre de conférences d’un hôtel international, nous avons passé deux grosses journées de visites guidées (balisées) dans les usines d’Intel à Penang et à Kulim (à 45 minutes de route l’une de l’autre).
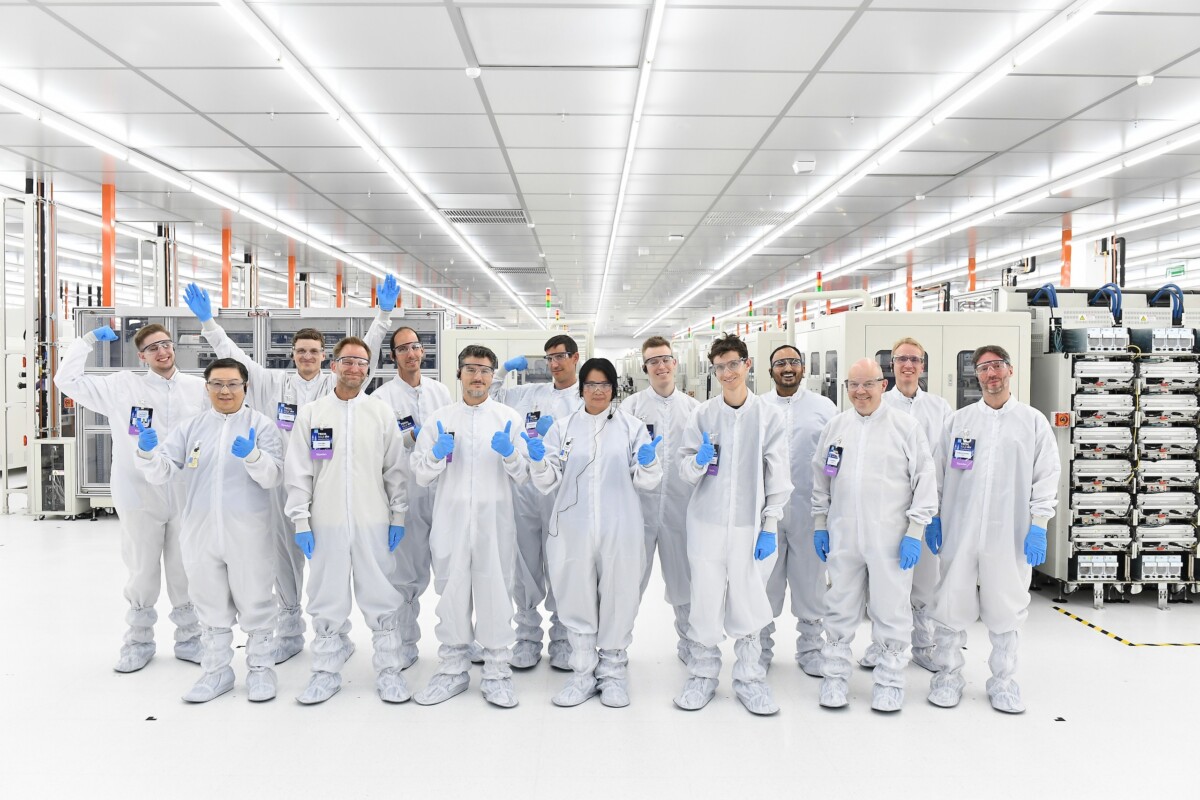
Les bâtiments abritent des bureaux, mais ils abritent surtout d’immenses « clean rooms », c’est-à-dire des salles blanches aux conditions d’accès strictes. Dans certaines zones, nous portons jusqu’à une « bunny suit » (combinaison de lapin) qui couvre intégralement la peau et les vêtements. Les surchaussures (avec bracelet antistatique), la combinaison intégrale, les gants, le masque, les lunettes et la capuche ne laissent que quelques centimètres carrés de peau exposés. Le code vestimentaire précise même qu’il faut attacher ses cheveux avec un élastique synthétique et pas en coton, duquel pourraient s’échapper des fibres.
Les employés peuvent entrer avec leur smartphone, mais faute de bloc-notes certifiés salles blanches, nous ne pouvons rien apporter. Les photos sont donc celles des photographes d’Intel qui nous ont accompagnés.
La visite peut commencer !
Die Sort & Die Preparation (DSDP)
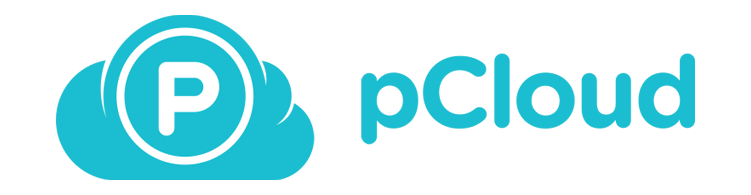
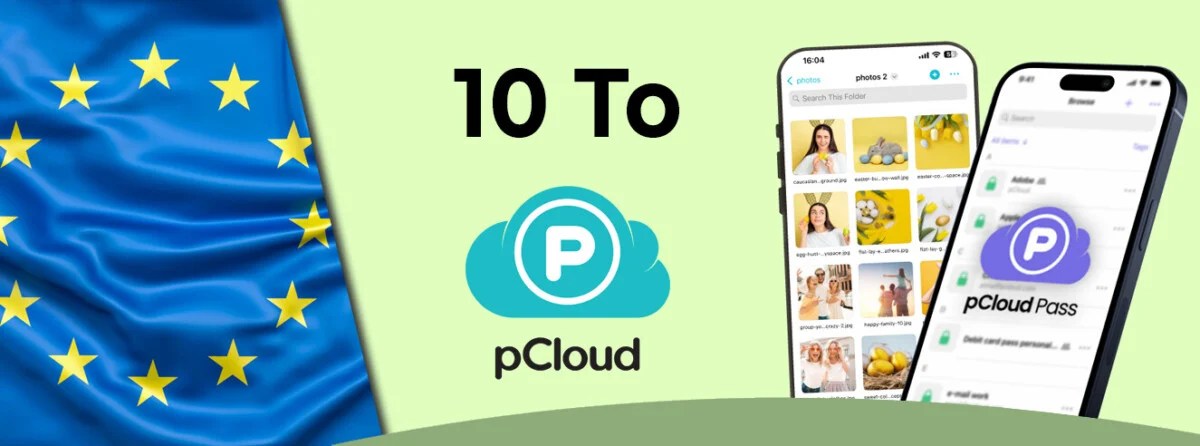
Découvrez les offres de pCloud : 2, 5 ou 10 To de stockage, situés dans des serveurs européen et sans abonnement, pour 5 personnes. Le gestionnaire de mots de passe est offert !
Dans ses usines malaisiennes, Intel reçoit les wafers provenant de ses usines des États-Unis (Oregon, Arizona, Ohio), d’Irlande, d’Israël et bientôt d’Allemagne, et les transforme en produits finis, prêts à emprunter différents canaux de distribution pour être livrés aux fabricants d’ordinateurs ou directement aux consommateurs.
Les wafers sont de fines galettes de silicium, de 300 mm de diamètre en l’occurrence, sur lesquelles on imprime par lithographie les milliards de transistors de dizaines de microprocesseurs, ici à une échelle de plus ou moins 7 nanomètres.
Die Singulation
La première étape est donc de séparer les microprocesseurs en découpant les wafers, dans l’usine Die Sort & Die Preparation de Kulim. Les wafers sont d’abord placés sur des supports constitués d’un film plastique qui perd son adhérence lorsqu’on l’expose aux UV. C’est la raison pour laquelle la zone est éclairée en jaune, sans UV.
Les wafers passent par une machine de gravure laser qui délimite les dizaines de dies, puis immédiatement après par une machine de die singulation (individualisation des puces), dans laquelle deux petites scies circulaires à lames en diamant découpent le wafer, mais pas le film plastique, à une vitesse étonnante compte tenu du niveau de précision micrométrique. Des jets d’eau assurent le refroidissement et l’évacuation des résidus. Dans une autre machine, le film est exposé à de la lumière UV pour perdre son adhérence tandis qu’un bras robotisé attrape chaque puce par succion pneumatique pour les déposer sur un autre support.
Les supports étaient jusqu’alors transportés manuellement de machine en machine.
Die Sort
Dans la zone suivante en revanche, la lumière est blanche et ce sont des véhicules autonomes qui transportent les supports entre des unités de stockage mécanisées et les cellules de test.
Des dies de quelques centimètres carrés sont ainsi aiguillés vers d’immenses modules, constitués chacun de 20 cellules de test pesant chacune environ 500 kg. Ces modules s’enchainent presque à perte de vue et leur nombre est tenu secret.
Une carte amovible, fabriquée par Intel dans l’usine voisine, permet d’adapter chaque cellule aux puces à tester. Pour Meteor Lake, les cartes disposent d’une sorte de socket constitué d’approximativement 2 000 aiguilles plus fines qu’un cheveu. Les puces y subissent des tests électriques bas niveau, que nous avons chronométré à environ 30 secondes.
Les puces défectueuses sont jetées, les autres sont conditionnées en rouleaux avant d’être conduites dans l’usine Assembly and Test de Penang (PGAT).
Assembly and Test
Dans l’usine Assembly and Test de Penang, comme son nom l’indique, les puces sont assemblées et testées.
Assemblage
C’est ici que les dies prennent leur forme finale, qu’on qualifie vulgairement de « processeur ». Chaque die est d’abord fixé au substrat, ce PCB vert qui fait le lien entre le die et la carte mère de l’ordinateur via le socket. Ils passent pour cela dans une machine qui aligne parfaitement quelques milliers de microscopiques billes de soudure puis les fusionne par un procédé de thermo-compression à 300 °C.
Pour solidifier l’ensemble, on commence par injecter de la résine époxy pour combler par capillarité l’air subsistant entre le die et le substrat. Puis, s’il s’agit d’un processeur dit desktop, on applique un matériau d’interface thermique (thermal interface material) sur le die et on colle un dissipateur thermique intégré (integrated heatspreader) au PCB. S’il s’agit d’un processeur dit mobile, on colle seulement un cadre métallique, appelé stiffener (renfort), au PCB.
Physiquement, on a dès lors ce que le commun des mortels appelle un « processeur ». Mais on ne sait pas encore précisément de quel modèle de processeur il s’agit.
Tests et binning
En effet, les procédés de fabrication des semi-conducteurs sont si microscopiques qu’ils sont imparfaits. Ainsi, bien que tous les dies soient imprimés sur un même wafer avec le même masque lithographique, en pratique les résultats ne sont pas rigoureusement identiques.
Une fois assemblés, les processeurs subissent donc une nouvelle batterie de tests, à plus haut niveau, permettant non seulement de vérifier leur bon fonctionnement, mais aussi et surtout de les trier. C’est ce qu’on appelle le binning.
Les processeurs passent en parallèle dans des High-Density Burn-in testers, qui testent le bon fonctionnement des différents sous-composants (CPU, GPU…), ainsi que les tolérances à différentes fréquences, tensions électriques et températures de chaque exemplaire. Des processeurs issus d’un même wafer ou d’un même lot de production peuvent ainsi devenir des modèles différents. Selon les gammes, certains exemplaires peuvent devenir un Core 5 ou un Core 7, un série F dont on a désactivé le GPU défaillant, un série K débridé…
Une fois triés, les processeurs passent enfin par l’étape Platform Performance Verification, au cours de laquelle ils sont testés en conditions quasi réelles. C’est-à-dire sur des plateformes (cartes mères) et avec des systèmes d’exploitation (Windows, Linux), des charges de travail et des périphériques (virtuels) semblables à ceux des utilisateurs finals.
En cas de défaillance, certains processeurs subissent des diagnostics plus approfondis, qui feront l’objet d’un article dédié, non pour les réparer, mais pour identifier et corriger un éventuel défaut de conception.
Livraisons fin 2023/début 2024
Les processeurs qui ont réussi toutes les épreuves peuvent passer aux toutes dernières étapes, que nous n’avons pas vues, pour être conditionnés et livrés aux clients, soit les fabricants d’ordinateurs (OEM), soit directement les utilisateurs finals.
Dans le cas de Meteor Lake, nouvelle génération de processeur pour ordinateur portable haut de gamme, Intel est probablement en train d’expédier les premiers lots aux fabricants d’ordinateurs. Le lancement commercial est prévu le 14 décembre 2023, nous découvrirons alors le détail des modèles de processeurs, qui seront baptisés Core Ultra, et certainement les premiers ordinateurs portables à les adopter. En attendant, les usines continueront à produire des milliers de processeurs 24h/24, 7 j/7.
Notre émission Twitch SURVOLTÉS, c’est un mercredi sur deux de 18h à 20h : retrouvez-nous pour parler voiture électrique ou vélo électrique, autour de débats, d’interviews, d’analyses et de jeux !
Ce contenu est bloqué car vous n'avez pas accepté les cookies et autres traceurs. Ce contenu est fourni par Disqus.
Pour pouvoir le visualiser, vous devez accepter l'usage étant opéré par Disqus avec vos données qui pourront être utilisées pour les finalités suivantes : vous permettre de visualiser et de partager des contenus avec des médias sociaux, favoriser le développement et l'amélioration des produits d'Humanoid et de ses partenaires, vous afficher des publicités personnalisées par rapport à votre profil et activité, vous définir un profil publicitaire personnalisé, mesurer la performance des publicités et du contenu de ce site et mesurer l'audience de ce site (en savoir plus)
En cliquant sur « J’accepte tout », vous consentez aux finalités susmentionnées pour l’ensemble des cookies et autres traceurs déposés par Humanoid et ses partenaires.
Vous gardez la possibilité de retirer votre consentement à tout moment. Pour plus d’informations, nous vous invitons à prendre connaissance de notre Politique cookies.
Gérer mes choix