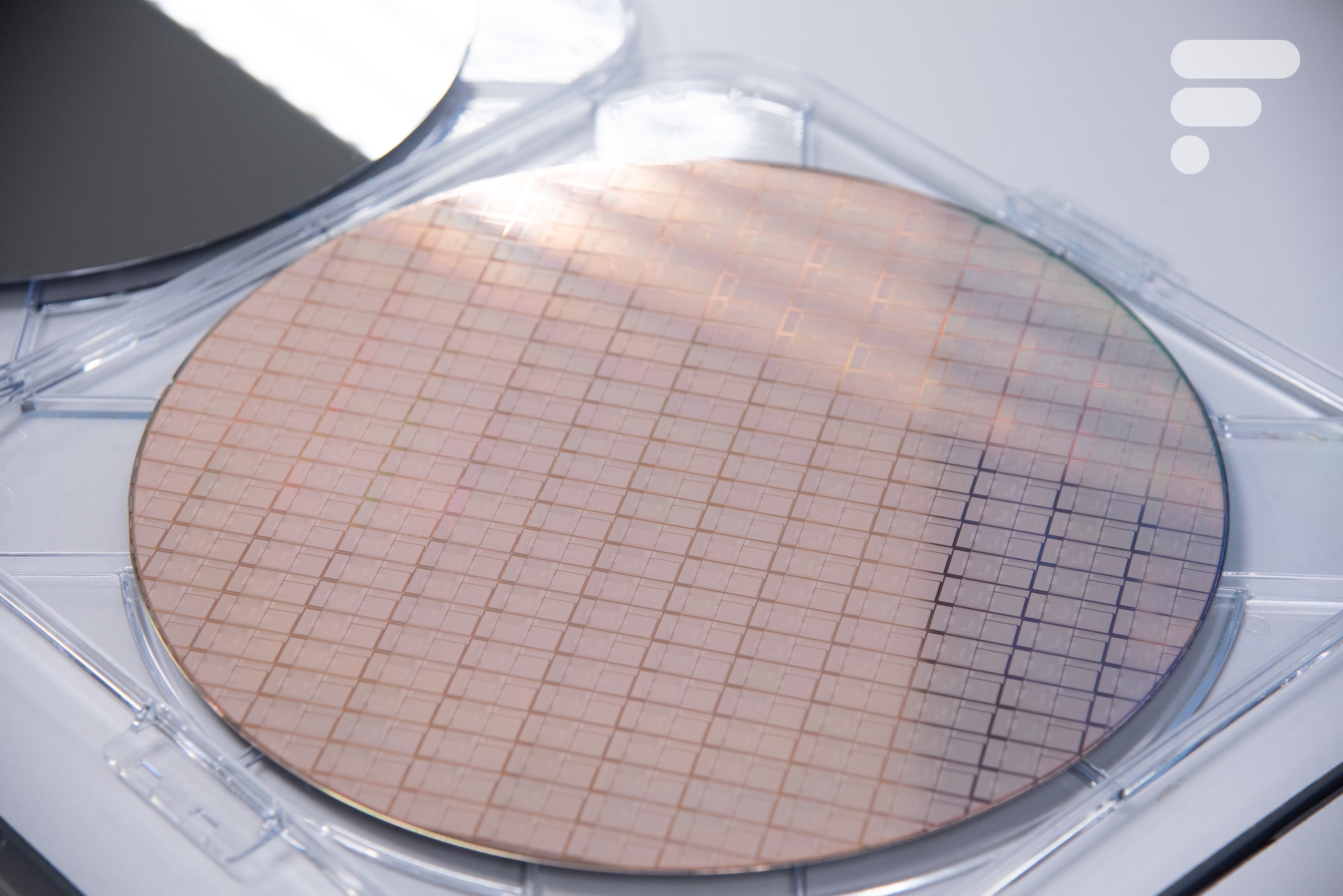
Dans un précédent article, nous avons vu comment les usines malaisiennes d’Intel transforment en processeurs les wafers fabriqués aux États-Unis, en Europe et en Israël. Mais contrairement à ce qu’on pourrait penser, les usines de ce qu’on appelait autrefois les pays du Sud ne se cantonnent pas à l’assemblage (qui est néanmoins et devient encore davantage une étape critique dans la production de puces, comme nous l’avons vu).
En effet, Intel Malaisie contribue activement à la conception des futurs processeurs, qui font de nombreux allers-retours entre le siège aux États-Unis, les fonderies des régions pré-citées et les salles blanches de Malaisie. Dans le cadre du voyage auquel Intel nous a invité, nous avons ainsi visité plusieurs laboratoires et ateliers essentiels au développement de nouveaux processeurs.
Design and Development Lab
Dans notre article précédent, nous avons détaillé les étapes d’assemblage de modèles de processeurs qui sont déjà commercialisés (Sapphire Rapids) ou qui le seront prochainement (Meteor Lake). Nous avons vu que 100 % des puces sont testées dans le cadre de ce processus quasi entièrement automatisé, non seulement pour exclure les exemplaires défaillants, mais aussi pour déterminer quelles puces d’un même lot peuvent devenir quelle référence de processeur (Core 3, 5, 7 ou 9, avec ou sans GPU, débridée ou non…).
Mais avant de lancer la production de masse, les usines malaisiennes d’Intel testent aussi à une autre échelle des processeurs encore en développement, dans son « laboratoire de design et développement », attenant aux chaines de production. Ici, des dizaines, voire des centaines d’ordinateurs « open bench » sont alignés sur plusieurs allées et plusieurs rangées de tables de laboratoire. Les processeurs « engineering sample » y sont soumis à des tests de montée en charge et à des tests de compatibilité avec toutes sortes de composants (mémoire vive, SSD, GPU…) et de périphériques (écrans, claviers, souris, supports de stockage, webcams…). Des cartes mères spéciales permettent de désactiver certaines fonctions précises pour isoler la cause des problèmes éventuels.
D’autres bancs de test, équipés d’un système de refroidissement liquide centralisé, servent à tester et à ajuster les spécifications thermiques et électriques (tension…) des futurs processeurs. On teste les processeurs de -10 °C jusqu’à 10 % au-delà de leur « Tjunction max », la température à partir de laquelle ils brident leurs performances pour éviter la surchauffe. La Tjmax est souvent de 100 ou 105 °C. Les ingénieurs peuvent régler « des centaines de paramètres architecturaux » en fonction des résultats.
Plus loin, on vérifie l’intégrité des signaux électriques et la conformité aux spécifications, par exemple du bus PCI-Express, à l’aide de générateurs de formes d’onde et d’oscilloscopes à haute bande passante. Sur la photo ci-contre, le signal ne traverse pas l’« œil » vert au centre, donc le test est réussi.
Le laboratoire fournit enfin des services aux « OEM », c’est-à-dire aux fabricants d’ordinateurs (Lenovo, Dell, HP…), afin de contribuer au développement des modèles adoptant les nouvelles générations de processeurs.
Failure Analysis Lab
Tester des centaines de processeurs, des premiers échantillons jusqu’à la montée en régime de la production de masse, permet de détecter et de corriger des défauts de conception ou de procédé de fabrication. En cas de problème, le processeur encore en développement subit un diagnostic approfondi, à bas niveau, à la recherche de la « root cause » (littéralement « cause racine »).
Les usines d’Intel en Malaisie intègrent pour cela un laboratoire dédié à l’analyse des défaillances, le « Failure Analysis Lab », dans lequel certains processeurs défaillants sont « autopsiés ». Les ingénieurs disposent d’un arsenal d’outils dignes de la police scientifique.
Ils disposent de microscopes permettant par exemple de déceler un mauvais alignement des billes de soudure entre le die et le substrat. Ils peuvent autrement injecter du courant par le biais de microsondes et utiliser de l’imagerie thermique pour déceler un court-circuit. Mais le plus impressionnant est un scanner à ultrasons capable de « voir » à travers un processeur pour détecter des imperfections entre ses couches, pour lequel on immerge le processeur dans quelques millimètres de liquide (d’eau ?).
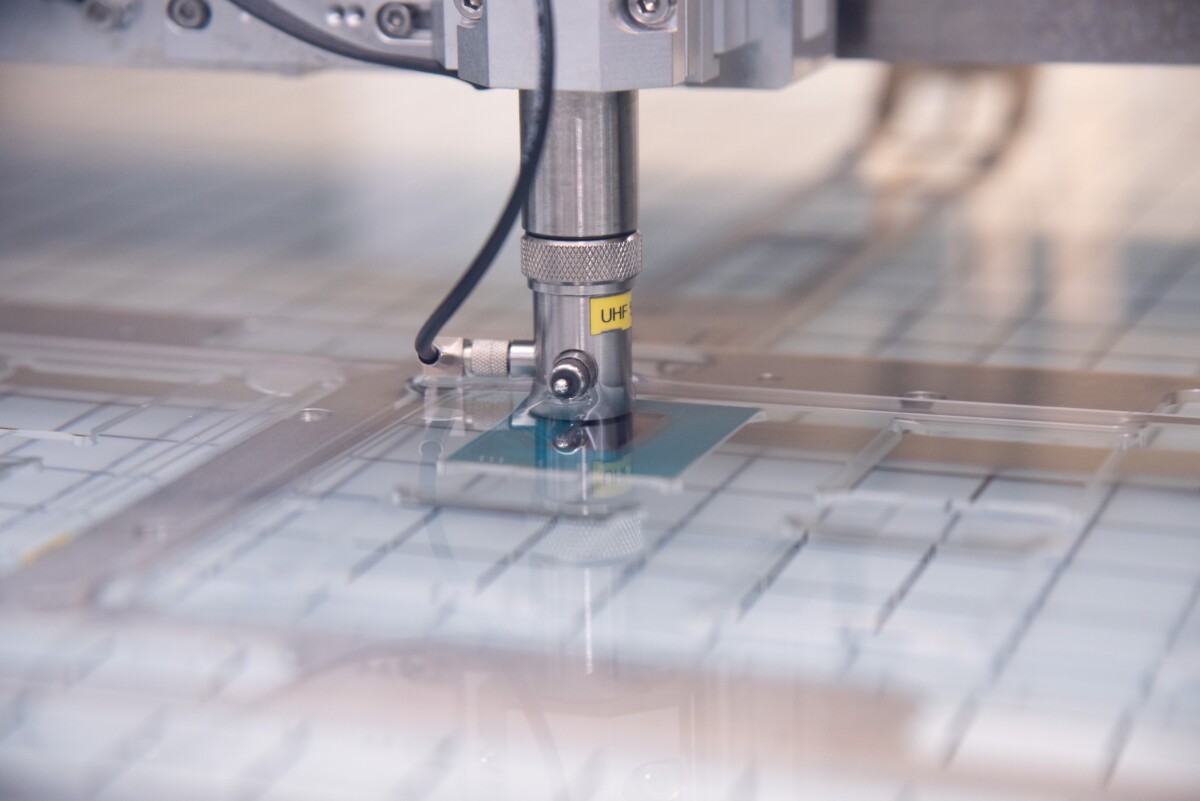
System Integration and Manufacturing Services
Le matériel décrit jusqu’à présent emploie certes des technologies de pointe, il est certes parfois spécifique, mais il provient néanmoins d’autres fabricants. Cela étant, pour certains besoins encore plus spécifiques ou pour des questions de secret industriel, Intel conçoit et fabrique parfois son propre matériel.
À Kulim, les usines d’Intel abritent ainsi les « System Integration and Manufacturing Services » (SIMS), littéralement les services de fabrication et d’intégration système, qui fabriquent et testent les équipements de test des processeurs.
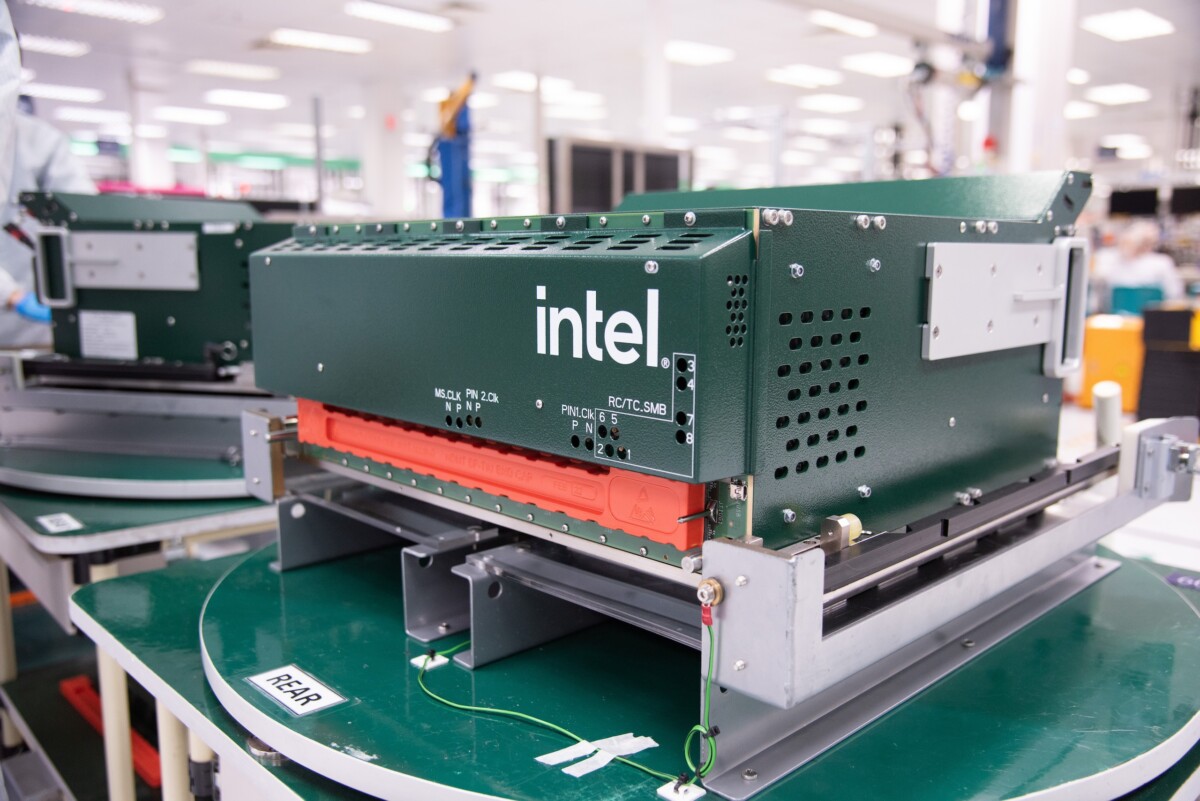
C’est notamment ici qu’Intel fabrique ses High Density Modular Tester (HDMT), les appareils qui testent et classent les puces (Core 5, 7, 9, etc.) dans les cellules de test, au moment du « die sort » décrit dans notre article précédent. Ces testeurs sont modulaires, car ils sont composés d’une part d’un boitier abritant l’électronique et d’autre part d’une (grande) carte amovible permettant de les adapter à tel ou tel socket de processeur.
La section SIMS fabrique aussi les High Density Burn-In Tester (HDBI), chargés des tests thermiques et électriques décrits au début de cet article, ainsi que les System Level Tester (SLT), qui testent les processeurs en conditions réelles, et les Reference Validation Platforms (RVP), les diverses cartes mères utilisées pendant le développement des processeurs pour les tests décrits tout au long de cet article.
La complexité d’un processeur
Nos deux articles de synthèse et de vulgarisation reflètent la complexité des processus de conception et de fabrication des processeurs, qui est à l’image de leur propre complexité. Ces innombrables équipements permettent, après autant d’étapes, de concevoir des processeurs de plus en plus puissants, de plus en plus efficients, et davantage ces dernières années depuis le grand retour d’AMD et l’expansion d’Apple sur le marché des semi-conducteurs.
Pour aller plus loin
Meteor Lake : bousculé par Apple, Intel lance sa plus grande révolution « depuis 40 ans »
Il nous reste néanmoins à relater l’étape la plus importante et la plus impressionnante de la fabrication d’un processeur : celle de la production des wafers, dans les « fabs » aux États-Unis, en Irlande ou en Israël. C’est pour rappel dans ces usines, peut-être les plus avancées sur Terre, qu’on « grave » à l’échelle nanométrique des milliards de transistors sur des galettes de silicium. Nous répondrons bien sûr « présent » si nous y sommes invités !
Retrouvez un résumé du meilleur de l’actu tech tous les matins sur WhatsApp, c’est notre nouveau canal de discussion Frandroid que vous pouvez rejoindre dès maintenant !
Ce contenu est bloqué car vous n'avez pas accepté les cookies et autres traceurs. Ce contenu est fourni par Disqus.
Pour pouvoir le visualiser, vous devez accepter l'usage étant opéré par Disqus avec vos données qui pourront être utilisées pour les finalités suivantes : vous permettre de visualiser et de partager des contenus avec des médias sociaux, favoriser le développement et l'amélioration des produits d'Humanoid et de ses partenaires, vous afficher des publicités personnalisées par rapport à votre profil et activité, vous définir un profil publicitaire personnalisé, mesurer la performance des publicités et du contenu de ce site et mesurer l'audience de ce site (en savoir plus)
En cliquant sur « J’accepte tout », vous consentez aux finalités susmentionnées pour l’ensemble des cookies et autres traceurs déposés par Humanoid et ses partenaires.
Vous gardez la possibilité de retirer votre consentement à tout moment. Pour plus d’informations, nous vous invitons à prendre connaissance de notre Politique cookies.
Gérer mes choix