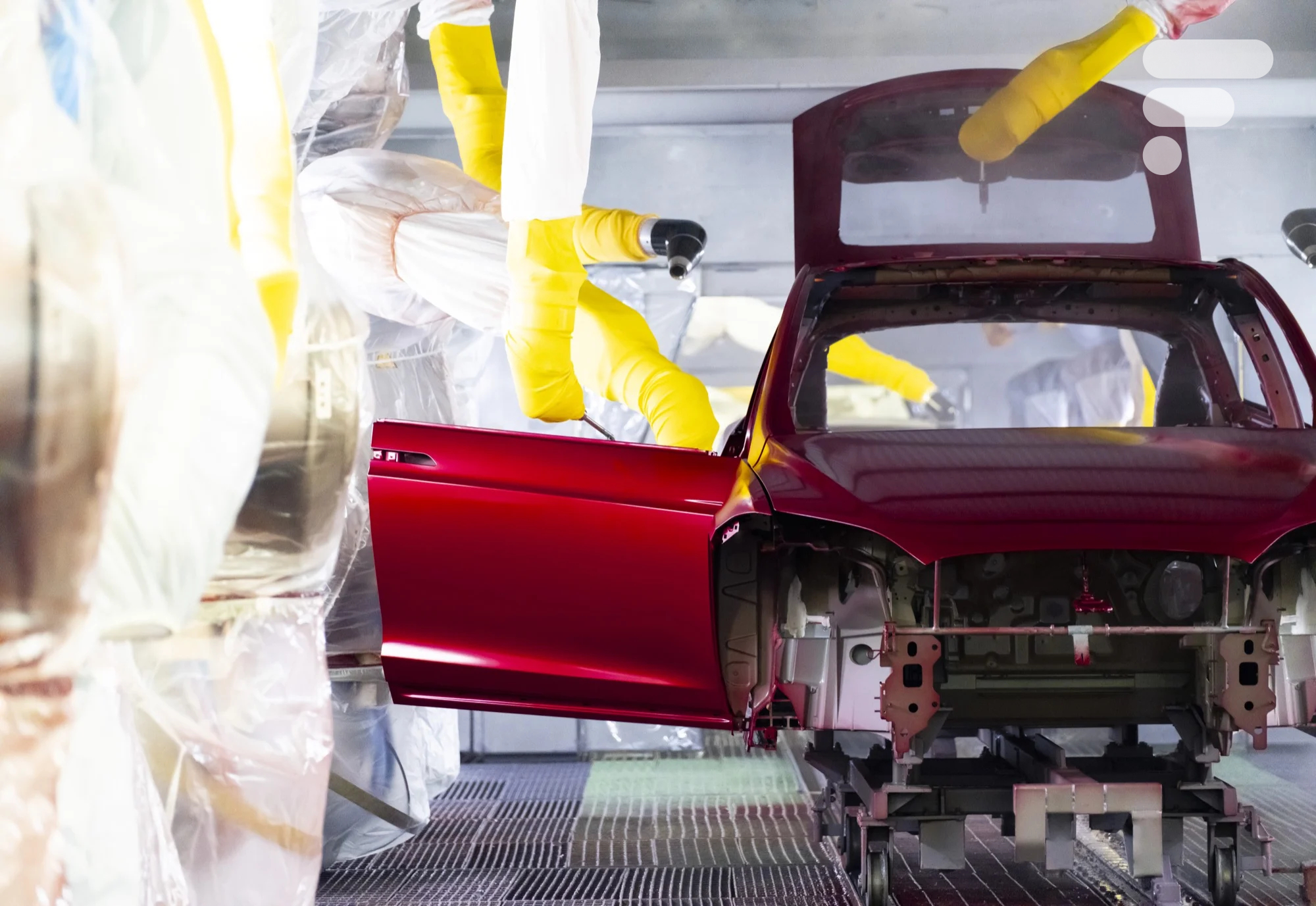
Selon les informations du média chinois Shanghai Securities News, la Gigafactory de Tesla à Shanghai intègre une technologie de pointe dans le processus de production du Model Y : la technologie Gigacast 2.0, qui sera aussi utilisée par la future Tesla Model 2.
La technique innovante de moulage sous pression d’une seule pièce (Gigacast 2.0) serait utilisée pour fabriquer le soubassement arrière monobloc du véhicule. Selon Cui Hailun, cité par le média chinois, responsable des systèmes de gestion structurelle et thermique de Tesla Shanghai, cette approche consolide ce qui était autrefois un assemblage de multiples pièces (plus de 400) en une seule pièce.

Une technique déjà utilisée par Tesla en Allemagne et aux États-Unis pour la production de la Tesla Model Y, mais avec une méthode moins élaborée, qui nécessite encore deux pièces différentes (Gigacast 1.0).
Quels avantages de ce moulage sous pression ?
L’application de cette nouvelle méthode de moulage sous pression réduit le poids du châssis de plus de 10 % par rapport aux techniques traditionnelles, influençant positivement la consommation énergétique, et donc l’autonomie à basses vitesses. Outre les bénéfices en termes de poids, la méthode introduit également une réduction substantielle des coûts, avec une diminution de 40 % des dépenses liées à l’assemblage du plancher arrière.
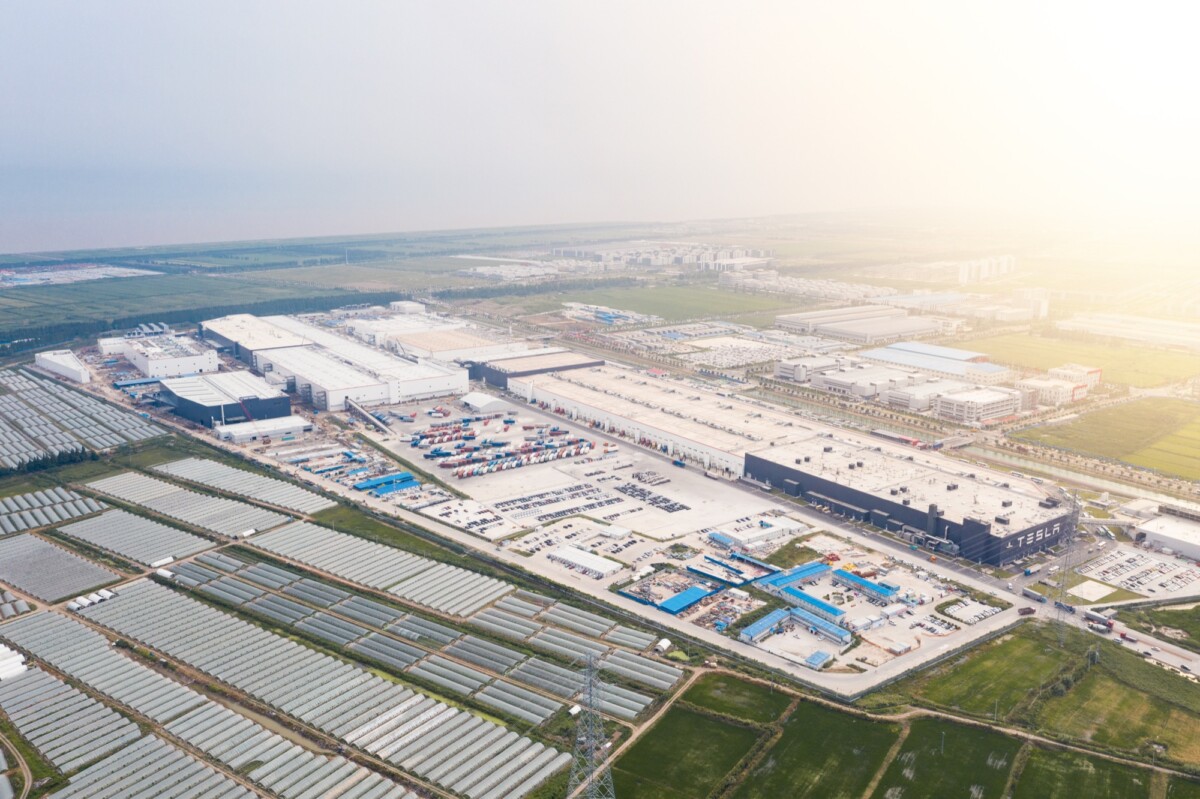
Ce procédé de moulage avancé n’est pas exclusivement utilisé par Tesla en Chine ; d’autres acteurs de l’industrie automobile locale ont également adopté des techniques similaires. Par exemple, Geely, avec sa marque Zeekr, a employé la technologie de moulage sous pression d’une seule pièce dans la conception de la carrosserie de son van Zeekr 009. Cela a permis d’éliminer près de 800 soudures et de réduire le nombre de pièces de plus de 80, tout en diminuant le poids total du châssis de 16 %.
De son côté, Xpeng, un autre constructeur automobile chinois, intègre des carrosseries avant et arrière monobloc en aluminium moulé sous pression dans sa plate-forme SEPA (Smart Electric Platform Architecture). Ce système de carrosserie avancé intègre 161 pièces et emploie une force de moulage sous pression impressionnante de 12 000 tonnes, optimisant ainsi la rigidité et la légèreté de la structure du véhicule.
Avec de tels avantages en termes de poids, de coûts et de productivité, la question de l’adoption généralisée de cette technologie de moulage sous pression d’une seule pièce se pose. Est-ce que les usines de Tesla à travers le monde utiliseront cette méthode à terme ? Il y a de fortes chances, même si la méthode Gigacast 1.0 permet déjà de nombreuses économies de production.
Des invités passionnants et des sujets palpitants ! Notre émission UNLOCK est à retrouver un mercredi sur deux en direct, de 17 à 19h sur Twitch. Pensez aussi aux rediffusions sur YouTube !
Ce contenu est bloqué car vous n'avez pas accepté les cookies et autres traceurs. Ce contenu est fourni par Disqus.
Pour pouvoir le visualiser, vous devez accepter l'usage étant opéré par Disqus avec vos données qui pourront être utilisées pour les finalités suivantes : vous permettre de visualiser et de partager des contenus avec des médias sociaux, favoriser le développement et l'amélioration des produits d'Humanoid et de ses partenaires, vous afficher des publicités personnalisées par rapport à votre profil et activité, vous définir un profil publicitaire personnalisé, mesurer la performance des publicités et du contenu de ce site et mesurer l'audience de ce site (en savoir plus)
En cliquant sur « J’accepte tout », vous consentez aux finalités susmentionnées pour l’ensemble des cookies et autres traceurs déposés par Humanoid et ses partenaires.
Vous gardez la possibilité de retirer votre consentement à tout moment. Pour plus d’informations, nous vous invitons à prendre connaissance de notre Politique cookies.
Gérer mes choix