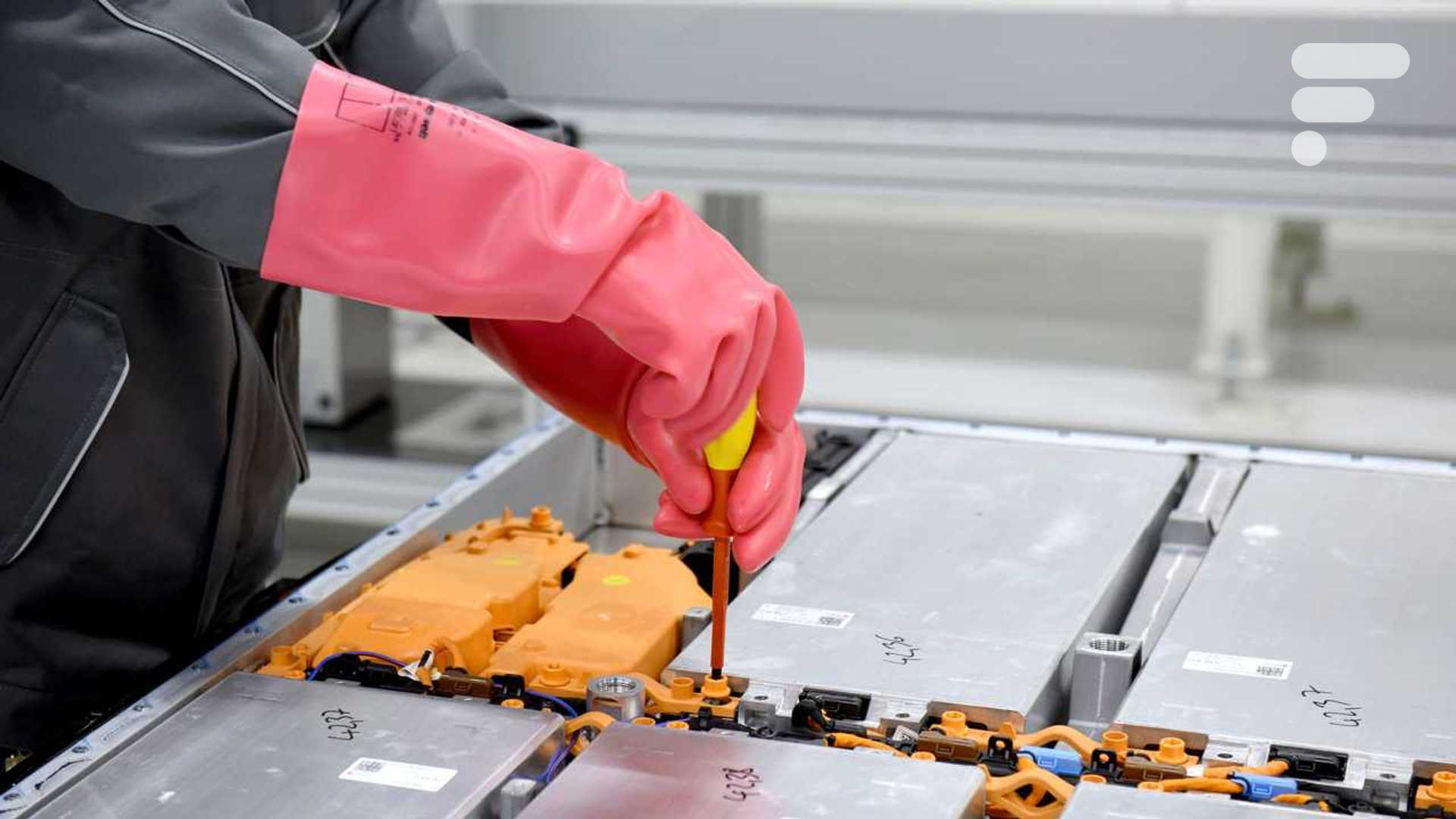
L’essor de la voiture électrique entraîne celui du marché des batteries, élément clé de la transition écologique. Mais produire de nouvelles batteries en quantités suffisantes pour répondre à la demande pourrait bientôt devenir difficile et contraignant en termes d’extraction et d’approvisionnement en matières premières. C’est aussi en partie pourquoi le recyclage des batteries usagées prendra de plus en plus de place d’ici les années à venir, sans parler de l’aspect purement écologique.
L’un des premiers à l’avoir compris est Jeffrey Brian Straubel, l’un des fondateurs de Tesla, qui a quitté la marque il y a quelques années pour se lancer dans l’aventure de la récupération et de la réutilisation des matériaux issus des batteries.
De son côté, l’Europe a également décidé d’investir massivement dans ces activités. Principalement parce qu’elle ne dispose pas encore d’une chaîne d’approvisionnement développée (la Chine ayant une hégémonie totale sur la production de batteries), qu’elle veut se libérer d’une dépendance vis-à-vis d’autres régions, mais aussi parce qu’elle a compris que c’est grâce au recyclage qu’il est possible de construire un secteur véritablement respectueux de l’environnement.
De plus en plus d’éléments seront recyclées
L’European Battery Alliance, association fondée en 2017 par le vice-président de la Commission européenne Maros Sefcovic, travaille à la définition même d’un marché circulaire et durable. Dans ce cadre, le recyclage joue un rôle clé. Avec les méthodes modernes, le pourcentage de matériaux pouvant être récupérés à partir des batteries en fin de vie dépasse facilement les 80 %. Mais il existe des techniques qui permettent de dépasser les 90 % et, dans certains cas, d’atteindre même 95 %.
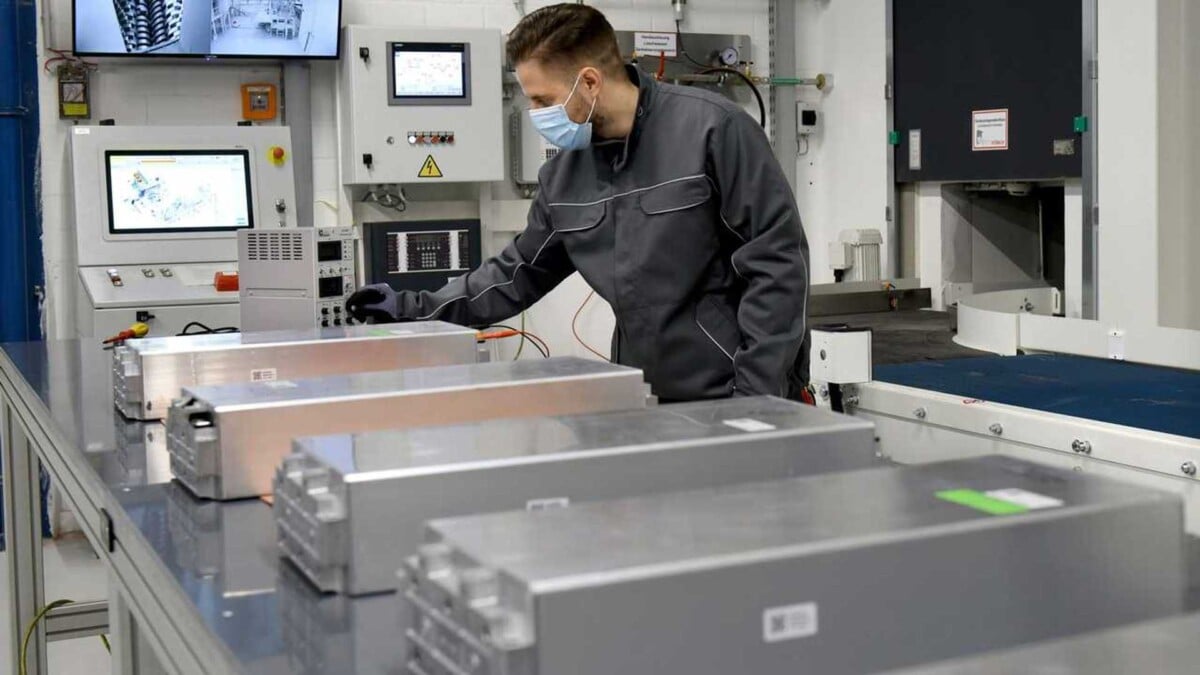
Il faut dire que les fabricants de batteries, précisément en raison de l’attention qu’ils portent au recyclage, conçoivent et fabriquent des accumulateurs qui seront plus faciles à recycler une fois leur vie utile terminée. À terme, cela permettra de réduire les coûts et d’obtenir de meilleurs résultats concernant leur recyclage.
Quand le législateur s’en mêle
L’été dernier, le Conseil européen a approuvé une directive stipulant que les fabricants doivent récupérer au moins 63 % des matériaux d’une batterie d’ici à 2027. Ce pourcentage doit passer à 73 % d’ici à la fin de 2030. Cette directive s’applique aux batteries en général.
En ce qui concerne les batteries lithium-ion, les objectifs fixés indiquent que ce taux doit atteindre 50 % d’ici 2027 et 80 % d’ici à la fin de 2031. Globalement, les constructeurs et les fabricants seront largement dans les clous au vu des chiffres déjà annoncés.
En outre, l’Union européenne a également introduit des niveaux minimaux obligatoires de matériaux recyclés à intégrer pour la production de nouvelles batteries industrielles plomb-acide et de batteries pour véhicules électriques. Ces niveaux sont de 85 % pour le plomb, 16 % pour le cobalt, 6 % pour le lithium et 6 % pour le nickel.
Un marché qui a de l’avenir
Si le recyclage des batteries joue encore un rôle marginal à ce jour, ce n’est pas seulement parce que cette industrie doit devenir plus mature. Dans les faits, à l’heure actuelle, la plupart des véhicules électriques en circulation sont récents et fonctionnent encore. Il commence à y avoir quelques cas concernant les premières générations de voitures électriques vendues à grande échelle, comme les Renault Zoé et les Nissan Leaf, mais les chiffres sont encore assez confidentiels.
Vous l’aurez compris, peu de batteries sont encore en fin de vie. Et il ne faut pas oublier que la plupart d’entre elles, même lorsqu’elles ne seront plus utilisées dans les véhicules électriques, trouveront d’autres utilisations dans les systèmes de stockage stationnaires.
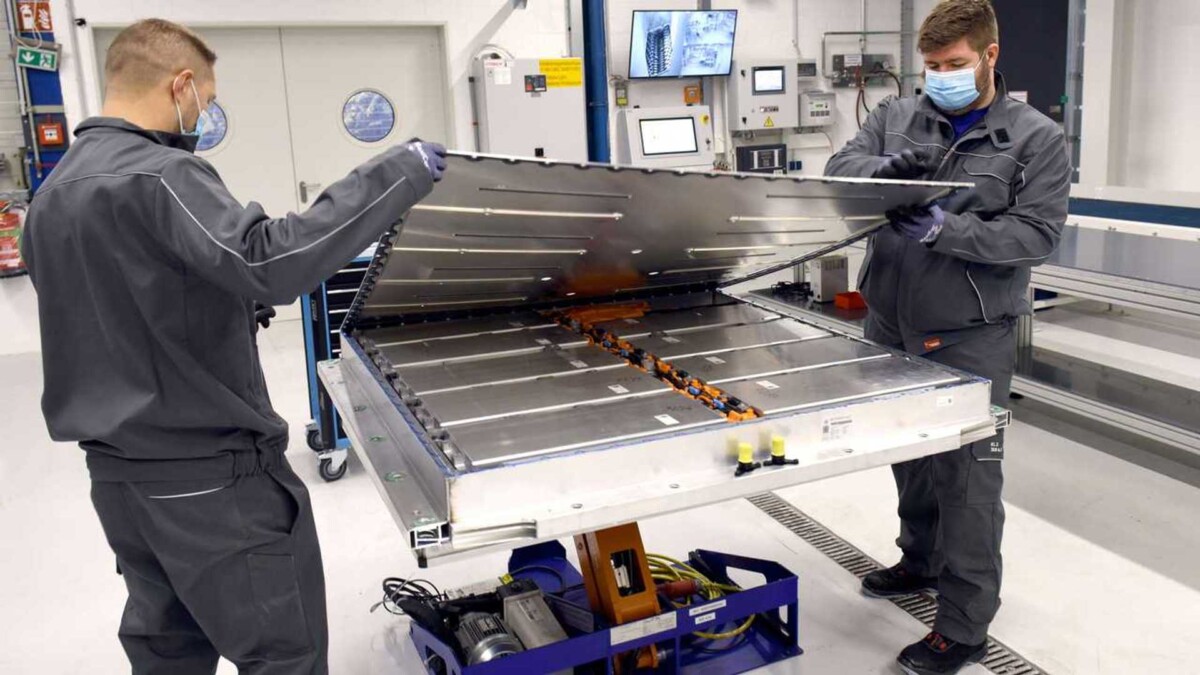
Si l’Europe fixe ses objectifs à l’horizon 2030, c’est notamment parce qu’à cette échéance, le Vieux Continent aura également la possibilité de créer un réseau de Gigafactories capables de répondre aux besoins du marché à grande échelle.
Actuellement, avec la Chine en position dominante, il n’est pas rare que la masse noire, c’est-à-dire l’ensemble des matériaux récupérés d’une batterie en fin de vie, soit collectée en Europe puis expédiée vers l’Est, où elle sera utilisée par des entreprises chinoises, sud-coréennes ou japonaises pour produire de nouvelles batteries.
Les techniques de recyclage utilisées
Passons désormais à quelque chose d’un peu plus technique. À l’heure actuelle, lorsque l’on parle de recyclage, on se réfère principalement à deux méthodes, qui sont les plus utilisées : la pyrométallurgie et l’hydrométallurgie.
- Pyrométallurgie : comme son nom l’indique, elle vise à séparer et à récupérer des matériaux individuels en exploitant des températures élevées. Pour simplifier, une batterie est placée dans un haut fourneau et des températures spécifiques sont atteintes pour obtenir des matériaux purs ou des alliages de matériaux qui peuvent être utilisés dans de nouveaux processus de production.
- L’hydrométallurgie : cette méthode, plus récente mais qui se développe à vitesse grand V, consiste à séparer les matières premières d’une batterie par l’utilisation de solvants chimiques. Se déroulant à basse température, elle nécessite moins d’énergie et est donc plus efficace. Surtout si, comme c’est de plus en plus le cas, les solvants utilisés sont fabriqués sans l’adoption (ou avec l’adoption en quantités réduites) de substances très polluantes.
Qui sont les constructeurs qui travaillent autour du recyclage des batteries ?
Parmi les plus importants constructeurs de voitures électriques, Tesla a de son côté créé son propre procédé de recyclage. Un procédé développé en interne en 2020 et mis en place à la Gigafactory du Nevada à la fin de cette même année. Cette technique lui permet ainsi de recycler 92 % des matières premières utilisées dans ses batteries d’après un rapport publié par l’entreprise elle-même en 2021.
Pour le moment, les chiffres sont encore assez modestes. En cette même année 2021, Tesla a recyclé 300 tonnes de cuivre, 200 tonnes de cobalt et 1500 tonnes de nickel. C’est mieux que rien, mais cela rejoint notamment l’un des points que nous avons souligné un peu plus haut. En effet, Tesla commence à peine à recycler les batteries de ses premiers modèles, et en particulier de sa Model S lancée en 2013.
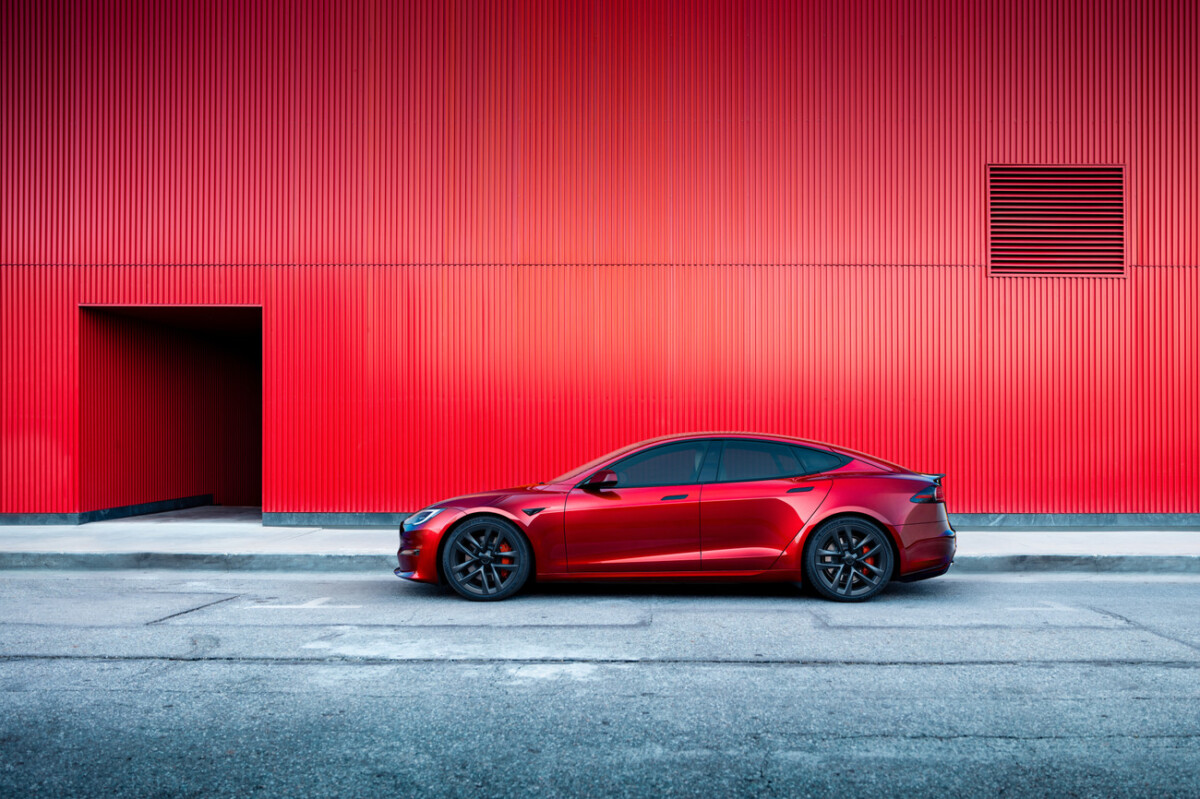
C’est actuellement la seule à pouvoir atteindre un stade suffisamment avancé au cours de son cycle de vie pour recycler sa batterie. D’ici la fin de la décennie 2020, le flux d’accumulateurs à recycler devrait considérablement augmenter au vu des chiffres de ventes du constructeur à travers le monde.
Il y environ un an, Mercedes a annoncé l’inauguration de sa toute nouvelle usine dédiée au recyclage des batteries. Située en Allemagne, dans la ville de Kuppenheim, celle-ci va alors se consacrer à 100 % au démantèlement des accumulateurs des voitures du constructeur.
Le développement du nouveau site se déroulera en plusieurs phases. L’usine se concentre sur le démantèlement mécanique depuis la fin de l’année dernière. Des pourparlers sont déjà en cours pour envisager une expansion et de nouvelles activités, notamment l’hydrométallurgie. Cette initiative permettrait à Mercedes de recycler les batteries de ses véhicules sur place, économisant ainsi du temps et de l’argent en réduisant la logistique.
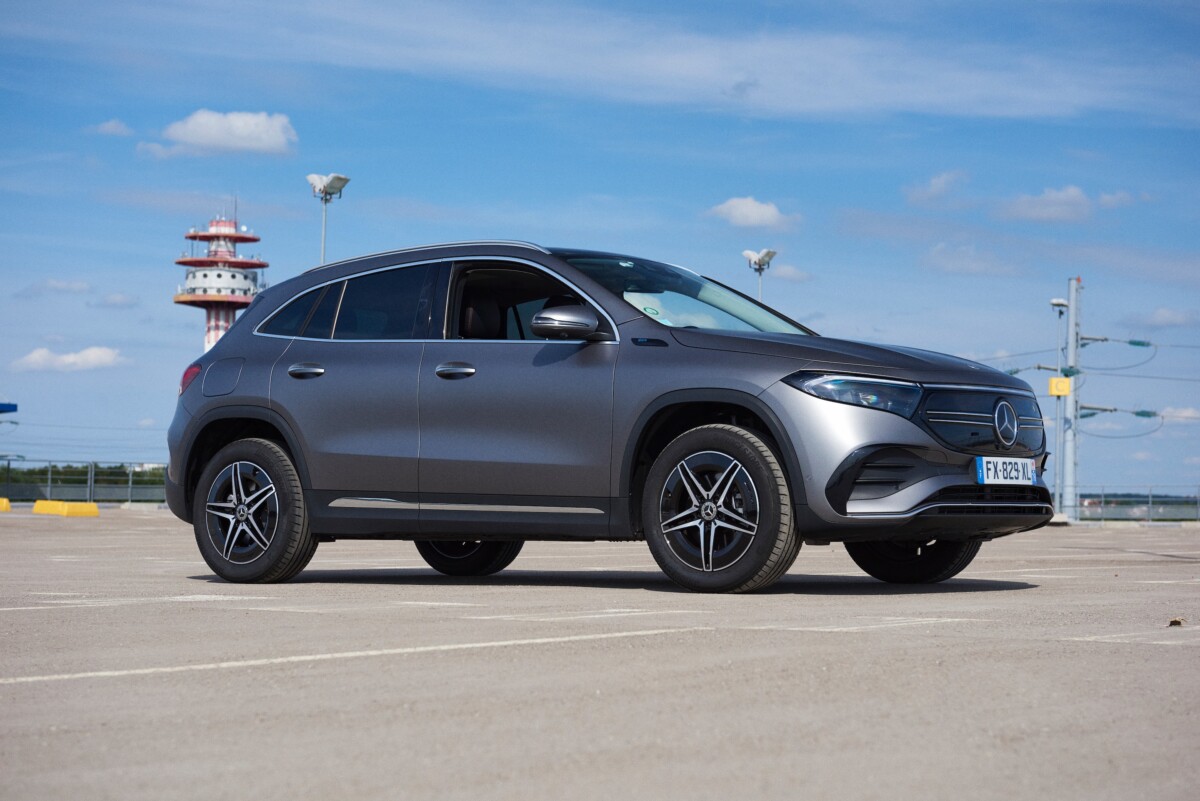
La marque serait en mesure d’atteindre un taux de recyclage allant jusqu’à 96 %, un record à l’heure actuelle. Le constructeur dépasserait alors Redwood Materials, qui a annoncé les résultats de son expérimentation lancée il y a deux ans et qui pourrait revaloriser les batteries jusqu’à 95 %.
Là encore, Mercedes annonce que son usine pilote devrait pouvoir recycler 2 500 batteries par an, permettant de produire environ 50 000 modules destinés à des voitures électriques de la marque. C’est faible, mais l’explication est la même que chez Tesla : il n’y a tout simplement pas assez de batteries à recycler pour l’instant.
Ça bouge aussi chez Volkswagen, même s’il y a un peu moins de chiffres annoncés. Le groupe compte prendre de l’avance sur ce terrain en annonçant la mise en place d’un projet de recyclage des batteries. L’idée du géant allemand est de réussir à recycler à l’infini (ou presque) les batteries sans aucune perte.
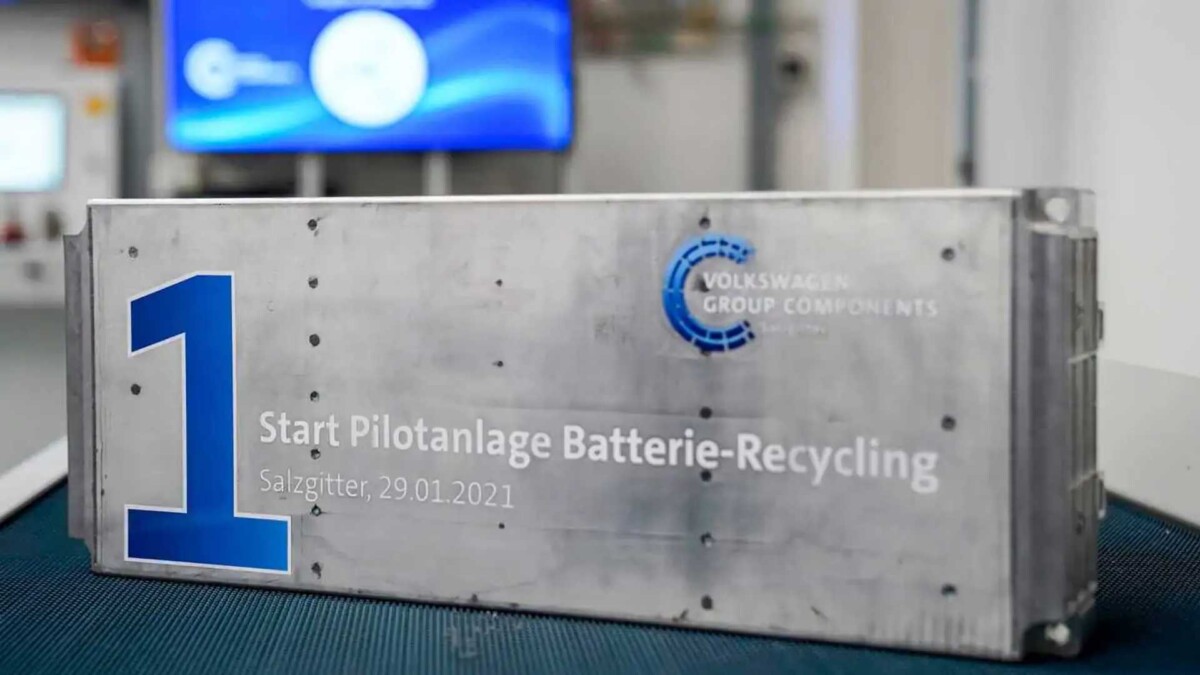
Pour le moment, on peut encore qualifier ce projet d’utopique, puisque les procédés de recyclage actuels présentent tous des pertes plus ou moins élevées. Sans compter que le recyclage détériore la pureté des matériaux et donc leur efficacité.
Du côté des fournisseurs de batteries, cela bouge aussi. La firme chinoise CATL prévoit de construire plusieurs usines de recyclage de batteries en Europe. Elle possède déjà deux sites d’assemblages sur le territoire et serait en mesure de valoriser certains éléments à 99 %. Selon le patron de l’entreprise, CATL serait déjà premier dans ce domaine, puisque celle-ci serait capable de valoriser 99 % des matériaux principaux des batteries NMC (nickel — manganèse — colbalt) et 90 % du lithium.
Et la France dans tout ça ?
L’année dernière, les entreprises Suez et Eramet se sont associées afin de mettre sur pied un projet d’usine de recyclage de batteries. Cette dernière sera implantée à Dunkerque et devrait être opérationnelle à partir de 2027. Là encore, les deux entités restent assez évasives sur les chiffres, mais dans un communiqué, elles affirment qu’elles utiliseront un « procédé innovant ». Ce dernier permettra « d’atteindre, voire de dépasser, les exigences de la future réglementation européenne en termes de recyclage, avec une utilisation des ressources naturelles et une empreinte carbone réduite ».
Cette technique, dont le détail n’a pas été dévoilé, sera d’abord testée à petite échelle dans le centre de recherche d’Eramet situé à Trappes, en région parisienne. En 2025, la construction l’usine de recyclage démarrera à Dunkerque. Elle sera opérationnelle à partir de 2027.
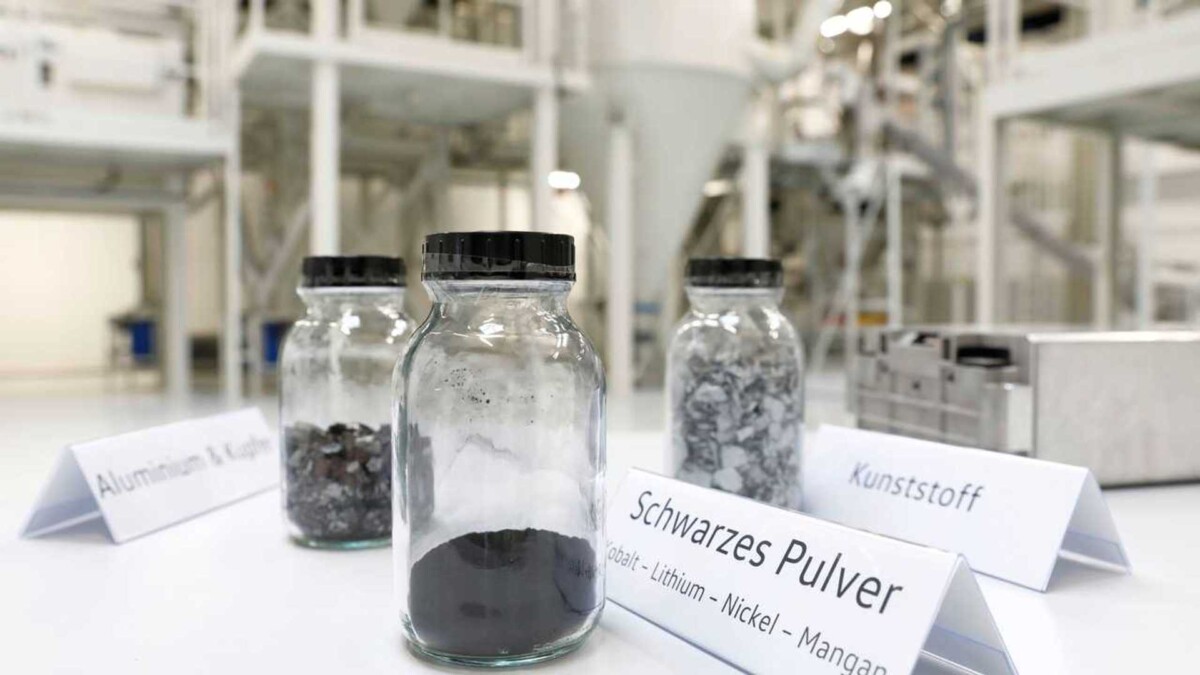
Pourquoi Dunkerque d’ailleurs ? L’emplacement n’a pas été choisi au hasard, puisque la ville accueillera aussi l’usine d’Envision, qui produira les batteries pour les futures voitures électriques de Renault. Le site dédié au recyclage se divisera en deux pôles : l’un qui s’occupera du démantèlement des batteries, avec une capacité de 200 000 par an environ, l’autre sera chargé d’extraire et d’affiner les matériaux comme le lithium ou encore le cobalt.
Ces derniers composent notamment la blackmass citée un peu plus haut dans notre dossier, une poudre noire obtenue en broyant les cellules des batteries. Ensuite, cette dernière est revalorisée afin d’en créer de nouvelles, ce qui devrait permettre de pallier risque de pénurie.
Chaque matin, WhatsApp s’anime avec les dernières nouvelles tech. Rejoignez notre canal Frandroid pour ne rien manquer !
Ce contenu est bloqué car vous n'avez pas accepté les cookies et autres traceurs. Ce contenu est fourni par Disqus.
Pour pouvoir le visualiser, vous devez accepter l'usage étant opéré par Disqus avec vos données qui pourront être utilisées pour les finalités suivantes : vous permettre de visualiser et de partager des contenus avec des médias sociaux, favoriser le développement et l'amélioration des produits d'Humanoid et de ses partenaires, vous afficher des publicités personnalisées par rapport à votre profil et activité, vous définir un profil publicitaire personnalisé, mesurer la performance des publicités et du contenu de ce site et mesurer l'audience de ce site (en savoir plus)
En cliquant sur « J’accepte tout », vous consentez aux finalités susmentionnées pour l’ensemble des cookies et autres traceurs déposés par Humanoid et ses partenaires.
Vous gardez la possibilité de retirer votre consentement à tout moment. Pour plus d’informations, nous vous invitons à prendre connaissance de notre Politique cookies.
Gérer mes choix